In the Merchant Navy, a cadet is an unlicensed trainee officer or engineer under training in much the same way as the military context. All Cadets receive training in firefighting, first aid and survival techniques.
Cadets choose either one of two branches for professional development. Deck cadets train in the fields of navigation, shiphandling and cargo handling as well as maritime law. Engine cadets train to become marine engineers, and as such their fields encompass a range of theoretical and practical engineering subjects, including Mechanical engineering, thermodynamics, control engineering, applied mathematics, welding and fabrication. Engineering practice is mostly learned during the cadet's assignment to a ship.
The cadet training scheme differs from country to country, but the learning objectives are always the same. In the UK for example, cadets undergo training in a block-release format, spending a shorter time in college before going to sea for a short assignment after which the cadet returns to college. Other countries allow the cadet to finish his/her degree before going to sea, but most countries seem to prefer a system where a cadet completes all of his/her sea time before returning to college for the final year of their degree.
Ship Engineering Officers Ranks (typical for a British Merchant Vessel – US equivalents in italics):
- Chief Engineer: In charge of the engine department. Reports only to the Master. The Chief Engineer's training, responsibility and rank are all superior to those required for a Chief Officer.
- Second Engineer 1st Assistant Engineer: In charge of the day-to-day running of the engine department. Often in charge of main engine maintenance. Takes the 4–8 watch. He is the equivalent of the Chief Mate.
- Third Engineer 2nd Assistant Engineer: Usually in charge auxiliary engines & boilers. Takes the 12–4 watch.
- Fourth Engineer 3rd Assistant Engineer: Usually in charge of air compressors, purifiers, pumps and other auxiliary machinery. Takes the 8–12 watch. Sometimes in charge of boilers.
- Electro-technical Officer (ETO): Officer who is responsible for the maintenance of electrical and electronic equipment.
- Electrical Officer: Officer who is responsible for the maintenance of electrical equipment, but not electronic equipment such as radars, VHF etc.
- Junior Engineer: No official responsibilities - this rank is reserved for those who are qualified as Fourth Engineers but lack the experience necessary to take a watch.
- Cadet: A trainee officer. Understudies the other engine department personnel.
Typically, a ship's engine department is run by the Engineering Officers but manned with other occupational specialties of the seafarer's trade like:
- Machinist/Fitter: A rating (or petty officer) who is specialized in fabrication, welding, etc.
- Motorman: A, not always, qualified engine rating who stands a watch with the Engineer Officer, as well as performing menial tasks and assisting Engineering Officers during maintenance.
- Oiler: A rating who is responsible for ensuring that machinery is adequately lubricated. Performs menial tasks such as cleaning, sounding tanks etc.
- Wiper: The lowest rating in the engine room and is tasked with keeping the machinery spaces clean and tidy. Wipers usually go on to become oilers once they are familiar with engine room machinery and specific routines.
- Stoker: Now defunct, the stoker was an engine department rating with responsibility for shoveling coal into the boiler furnaces.
- Coal Trimmer: Now defunct, the coal trimmer was an engine department rating with responsibility to load coal in the bunkers and to transport the coal from the bunkers to the stokers
10 Main Personal Protective Equipment (PPE) Used Onboard Ship
Following are the basic personal protective equipments (ppe) that are always present onboard a ship to ensure safety of the working crew:
1) Protective Clothing: Protective clothing is a coverall which protects the body of the crew member from hazardous substance like hot oil, water, welding spark etc. It is popularly known as “dangri “or “boiler suit”.
2) Helmet: The most important part of the human body is the head. It needs utmost protection which is provided by a hard plastic helmet on the ship. A chin strap is also provided with the helmet which keeps the helmet on place when there is a trip or fall.
3) Safety Shoes: Maximum of the internal space of the ship is utilized by cargo and machinery, which is made of hard metal and which make it clumsy for crew to walk around. Safety shoes ensure that nothing happens to the crew member’s feet while working or walking onboard.
4) Safety Hand gloves: Different types of hand gloves are provided onboard ship. All these are used in operations wherein it becomes imperative to protect ones hands. Some of the gloves provided are heat resistant gloves to work on hot surface, cotton gloves for normal operation, welding gloves, chemical gloves etc.
5) Goggles: Eyes are the most sensitive part of the human body and in daily operations on ship chances are very high for having an eye injury. Protective glass or goggles are used for eye protection, whereas welding goggles are used for welding operation which protects the eyes from high intensity spark.
6) Ear Muff/plug: Engine room of the ship produces 110-120 db of sound which is very high for human ears. Even few minutes of exposure can lead to head ache, irritation and sometimes partial or full hearing loss. An ear muff or ear plug is used on board ship which dampens the noise to a bearable decibel value.
7) Safety harness: Routine ship operation includes maintenance and painting of high and elevated surfaces which require crew members to reach areas that are not easily accessible. To avoid a fall from such heightened area, safety harness is used. Safety harness is donned by the operator at one end and tied at a strong point on the other end.
8) Face mask: Working on insulation surface, painting or carbon cleaning involves minor hazardous particles which are harmful for human body if inhaled directly. To avoid this, face mask are provided which acts as shield from hazardous particle.
9) Chemical suit: Use of chemicals onboard ship is very frequent and some chemicals are very dangerous when they come in direct contact with human skin. A chemical suit is worn to avoid such situations.
10) Welding shield: Welding is a very common operation onboard ship for structural repairs. A welder is provided with welding shield or mask which protects the eyes from coming in direct contact with ultraviolet rays of the spark of the weld.
MARPOL 73/78 is the International Convention for the Prevention of Pollution from Ships
Annex I
International Convention for the Prevention of Pollution of the Sea by Oil
Annex II
the elimination of pollution by noxious liquid substances carried in large quantities.
Annex III
It contains general requirements for the standards on packing, marking, labeling, documentation, stowage, quantity limitations, exceptions and notifications for preventing pollution by noxious substances.
Annex IV
It introduces requirements to control pollution of the sea by sewage from ships.
Annex V
Regulations for the Prevention of Pollution by Garbage from Ships.
Annex VI
It introduces requirements to regulate the air pollution being emitted by ships
Annex VII
It introduces requirements to regulate the Ballast
Auxiliary Marine Machinery
Diesel Engine
Four-stroke engine
A four-stroke engine (also known as four cycle) is an internal combustion (IC) engine in which the piston completes four separate strokes while turning a crankshaft. A stroke refers to the full travel of the piston along the cylinder, in either direction. The four separate strokes are termed:
- Intake: also known as induction or suction This stroke of the piston begins at top dead center (T.D.C.) and ends at bottom dead center (B.D.C.). In this stroke the intake valve must be in the open position while the piston pulls an air-fuel mixture into the cylinder by producing vacuum pressure into the cylinder through its downward motion.
- Compression: This stroke begins at B.D.C, or just at the end of the suction stroke, and ends at T.D.C. In this stroke the piston compresses the air-fuel mixture in preparation for ignition during the power stroke (below). Both the intake and exhaust valves are closed during this stage.
- Combustion: also known as power or ignition This is the start of the second revolution of the four stroke cycle. At this point the crankshaft has completed a full 360 degree revolution. While the piston is at T.D.C. (the end of the compression stroke) the compressed air-fuel mixture is ignited by a spark plug (in a gasoline engine) or by heat generated by high compression (diesel engines), forcefully returning the piston to B.D.C. This stroke produces mechanical work from the engine to turn the crankshaft.
- Exhaust: also known as outlet. During the exhaust stroke, the piston once again returns from B.D.C. to T.D.C. while the exhaust valve is open. This action expels the spent air-fuel mixture through the exhaust valve.
Two-stroke engine
A two-stroke, or two-cycle, engine is a type of internal combustion engine which completes a power cycle with two strokes (up and down movements) of the piston during only one crankshaft revolution. This is in contrast to a "four-stroke engine", which requires four strokes of the piston to complete a power cycle during two crankshaft revolutions. In a two-stroke engine, the end of the combustion stroke and the beginning of the compression stroke happen simultaneously, with the intake and exhaust (or scavenging) functions occurring at the same time.
Two-stroke engines often have a high power-to-weight ratio, power being available in a narrow range of rotational speeds called the "power band". Compared to four-stroke engines, two-stroke engines have a greatly reduced number of moving parts, and so can be more compact and significantly lighter.
Refrigeration
Refrigeration is a process of removing heat from low temperature reservoir and transferring it to high temperature reservoir. The work of heat transfer is traditionally driven by mechanical work, but can also be driven by heat, magnetism, electricity, laser, or other means. Refrigeration has many applications, including, but not limited to: household refrigerators, industrial freezers, cryogenics, and air conditioning. Heat pumps may use the heat output of the refrigeration process, and also may be designed to be reversible, but are otherwise similar to air conditioning units.
Refrigeration has had a large impact on industry, lifestyle, agriculture and settlement patterns. The idea of preserving food dates back to at least the ancient Roman and Chinese empires. However, mechanical refrigeration technology has rapidly evolved in the last century, from ice harvesting to temperature-controlled rail cars. The introduction of refrigerated rail cars contributed to the westward expansion of the United States, allowing settlement in areas that were not on main transport channels such as rivers, harbors, or valley trails. Settlements were also developing in infertile parts of the country, filled with newly discovered natural resources. These new settlement patterns sparked the building of large cities which are able to thrive in areas that were otherwise thought to be inhospitable, such as Houston, Texas, and Las Vegas, Nevada. In most developed countries, cities are heavily dependent upon refrigeration in supermarkets, in order to obtain their food for daily consumption. The increase in food sources has led to a larger concentration of agricultural sales coming from a smaller percentage of existing farms. Farms today have a much larger output per person in comparison to the late 1800s. This has resulted in new food sources available to entire populations, which has had a large impact on the nutrition of society.
Air compressor
working principles and operational guideline
Use of compressed air for ships machinery
Compressed air has many uses on board ship, ranging from diesel engine starting to the cleaning of machinery during maintenance. The air pressures of 25 bar or more are usually provided in multi-stage machines. Here the air is compressed in the first stage, cooled and compressed to a higher pressure in the next stage, and so on.
Type Of Pump
Positive Displacement Pump
Positive displacement pumps are self priming pumps and are normally used as priming devices.
- They consist of one or more chamber, depending upon the construction, and the chambers are alternatively filled and emptied.
- The positive displacement pumps are normally used where the discharge rate is small to medium.
- They are popularly used where the viscosity of the fluid is high.
- They are generally used to produce high pressure in the pumping system.
Dynamic Pressure or Roto-Dynamic Pump.
- In dynamic pressure pump, during pumping action, tangential force is imparted which accelerates the fluid normally by rotation of impeller.
- Some systems which contain dynamic pump may require positive displacement pump for priming.
- They are normally used for moderate to high discharge rate.
- The pressure differential range for this type of pumps is in a range of low to moderate.
- They are popularly used in a system where low viscosity fluids are used.
These broad classification of pumps are further differentiates by their constructional properties and popularity of usage onboard ship;
Positive Displacement pump:
- Reciprocating Pump
- Screw pump
- Gear pump
- Piston pump
- Ram type pump
- Vane pump
Dynamic pressure pumps:
- Centrifugal pumps
- Axial flow pumps
- Submersible pump
- Centrifugal-axial (mixed) pump
FWG (Fresh Water Generator)
Fresh water production from sea water for domestic and auxiliary purposes is an essential requirement aboard ships. A considerable amount of fresh water is consumed in a ship. The crew consumes an average 100 liter/head/day. In a steam ship (a ship whose main propulsion unit is steam turbine or a ship which is a large tanker having steam turbine driven cargo oil pumps) the consumption for the boiler can be as high as 30 tonnes/day.
Sufficient potable water may be taken on in port to meet crew and passenger requirement. But the quality of this water will be too poor for use in water tube boilers and for filling expansion tanks. It is common practice to take on only a minimum supply of potable water and make up the rest by distillation of sea water. The stowage space that would have been used for fresh water can hence be utilized for fuel or extra space made available for cargo when fresh water generator is installed on a ship. It is statutory requirement to have a distillation plant for emergency use if otherwise ship has carried sufficient potable water. The equipment used on board for the production of freshwater from seawater is known as fresh water generator.
Various types of fresh water generators used on board ships are mainly:
- Submerged tube type fresh water generator
- Plate type fresh water generator, and
- Reverse osmosis plant
What ever type of plant is used, essential requirement of any fresh water generator is that it should produce fresh water as economically as possible.
Submerged Tube Type Fresh Water Generator
The shell and tube freshwater generator consist of heat exchanger, separator shell and condenser. In addition to this water ejector, ejector pump, distillate pump, salinity indicator, demister or mesh separator, solenoid valve and water flow meter are also fitted as accessories.
Fresh Water Generator Working Principle
Basic principle of all low pressure freshwater generator is that, boiling point of water can be reduced by reducing the pressure of the atmosphere surrounding it. By maintaining a low pressure, water can be boiled at low temperatures say 50 degree Celsius. The source of heat for the fresh water generator could be waste heat rejected by main engine jacket cooling water.
Hence using energy from a heating coil, and by reducing pressure in the evaporator shell, boiling can takes place at about 40 to 60 degree Celsius. This type of single effect plant is designed to give better economy than obsolete Boiling Evaporators.
The submerged tube type fresh water generator explained below uses the heat from main engine jacket cooling water to produce drinkable water by evaporating seawater due to the high vacuum, which enables the feed water to evaporate at a comparative low temperature. Steam can also be used as a heat source instead of main engine jacket cooling water.
This type of fresh water generator is based on two sets of shell and tube heat exchangers, one acting as evaporator or heater and other as condenser.
The combined air/brine ejector creates evaporator chamber vacuum condition by driving sea water pass through air/brine ejector, and sea water supplied by the ejector pump to be delivered to ejector for taking out the brine (concentrated seawater) and air. A simple fresh water generator diagram is shown below.
While entering to the evaporator chamber temperature of feed water will be around 50 degree Celsius. Feed water supply rate to the evaporator is fixed by an orifice fitted at the feed inlet. Because of the vacuum condition inside evaporator feed water evaporates at this temperature. The water spray and droplets are partly removed from the vapour by the deflector mounted on top of the evaporator and partly by a build in demister. The separated water droplets fall back into the brine, which is extracted by the water ejector.
The desalted vapour, which passes through the demister, will come in contact with the condenser, where it will be condensed by means of incoming cold seawater.
The distilled water is then taken out by integral freshwater pump (distillate pump) and controlled by salinometer and solenoid valve. If the salt content of produced water is high, solenoid valve diverts the freshwater to the shell side of freshwater generator, and issues an alarm signal. In order to get better suction head, distillate pump is placed at the lowest possible location in the fresh water generator plant. This is because the fresh water generator shell is at a lower pressure. Distillate pump get maximum net positive suction head with the height of liquid column in the suction line.
Thermometers are installed for control of seawater to the condenser and jacket cooling water to the evaporator. These thermometers permit control of both heating and cooling of these units. The salinometer or salinity indicator is connected to remote alarm so that very high salinity is immediately registered at the engine control room of the ship.
A detailed line diagram of a tube type fresh water generator on board ship is shown below. Click on the diagram to enlarge.
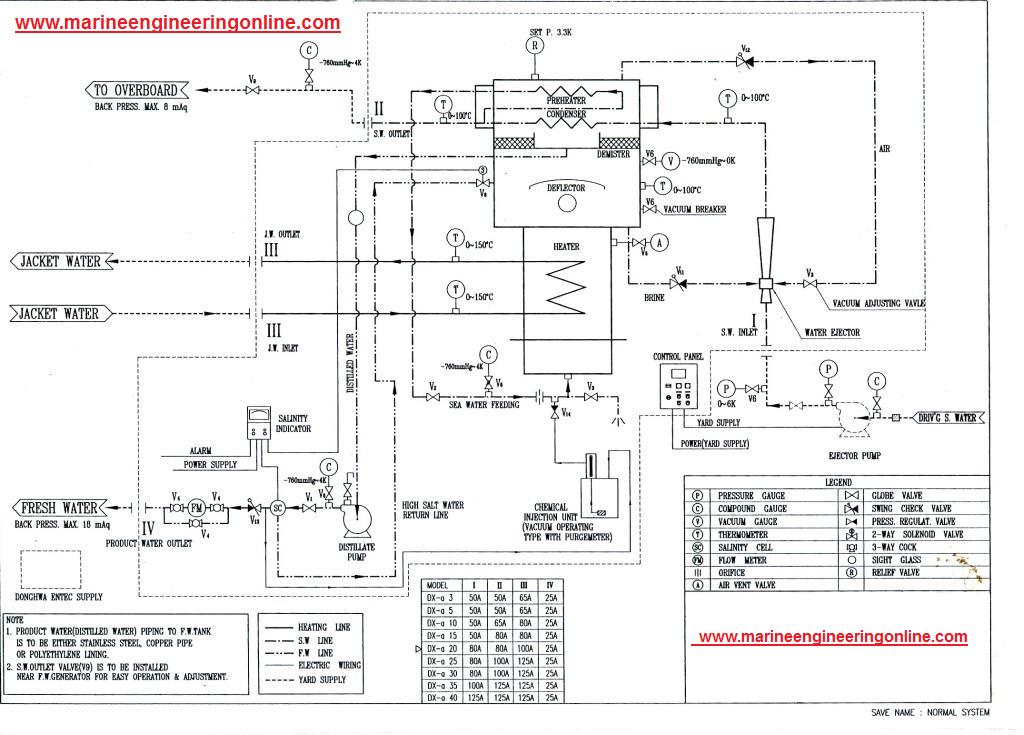
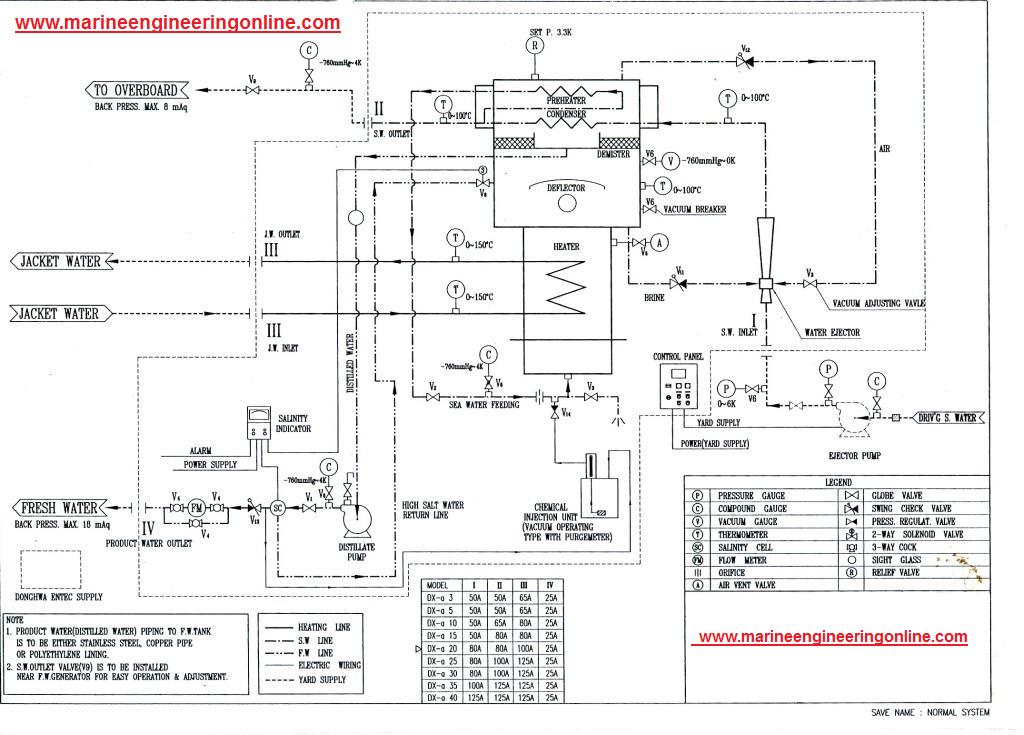
Plate Type Fresh Water Generator
Working principle of plate type fresh water generator is same as that of submerged tube type. Only difference is the type of heat exchangers used. Here plate type heat exchangers are used for condenser and evaporator unit. Heat from the diesel engine cooling water is used to evaporate a small fraction of the seawater feed in the plate type freshwater generator or evaporator. Unevaporated water is discharged as brine (by combined air /brine ejector). The evaporated water passes through the demister to the plate type vapour condenser. Here, after condensation it is discharged to fresh water storage tank by fresh water distillate pump. During entire operation the feed rate to the evaporator is fixed by the orifice plate at the feed inlet to evaporator. A typical plate type freshwater generator line diagram is shown below.
In the event of salinity of fresh water exceeding a predetermined value (maximum usually 10 ppm) the solenoid controlled dump valve diverts the flow back to the shell. This prevent contamination of the made water. Excess salinity could be used by many factors include leakage of seawater at condenser or priming of evaporator or malfunctioning of demister, or many other reasons.
What cannot be condensed at the condenser are called ‘incondensable gases’ like air and these gases are continuously ejected out by air/brine ejector. This way the shell of fresh water generator is maintained at high vacuum, a must requirement to boil water at low temperatures.
Materials of Construction for Fresh Water Generator
The shell is usually fabricated steel (or non-ferrous metal like cupro-nickels) which has been shot blasted then coated with some form of protective. One type of coating is sheet rubber which is rolled and bonded to the plate then hardened afterwards by heat treatment. The important points about protective coatings are:
- They must be inert and prevent corrosion.
- They must resist the effect of acid cleaning and water treatment chemicals
- They must have a good bond with the metal
Heat exchangers use aluminium brass tubes and muntz netal tube plate in the case of tube type fresh water generator. For plate type, titanium plates are used for condenser and evaporator. Demister is made of layered knitted wire of monel metal.
Operation
Extreme care must be taken during the operation of fresh water generator onboard ships. Operate all the valves gradually. Sudden opening and closing of valves may result in thermal shock to the main engine. Also make sure that distillate pump never runs dry.
Fresh water Generator Starting Procedure
- Make sure seawater ejector pump suction, discharge and overboard valves are open. Start the ejector pump. Seawater pressure at the air ejector must be 3 bar or more.
- Wait for vacuum to build up inside fresh water generator shell. (About 92 % vacuum).
- Open the feed water valve to feed seawater to the evaporator. Adjust the feed water pressure. Normally marking is provided on the pressure gauge for desired feed water pressure.
- Open main engine jacket cooling water inlet and outlet to the evaporator gradually.
- Open the air vent clock at the top of the evaporator to make sure the evaporator is filled with jacket cooling water. Air must be purged out if any.
- Switch on the salinity alarm panel for measuring purity of the freshwater produced.
- There will be a sight glass provided at the suction line for the distillate pump. Make sure condensed water is coming to the suction line. Now start the distillate pump and open discharge valve to lead generated water to specified storage tanks.
- Do checks While Running Fresh water Generator
- Through the sight glass provided in the evaporator shell, observe flashing of water.
- Also check for the brine level inside. It should not be too high or too low.
- Shell temperature must be around 50 deg cel.
- Make sure shell vacuum is more than 90% from the vacuum gauge.
- Check seawater inlet and outlet temperature to the condenser.
- Ensure seawater pressure at air ejector inlet more than 3 bars.
- Check for distillate pump pressure and water flow meter.
- Check salinity of fresh water produced.
- Check level and flow of dosing chemical.
- Check ampere of ejector pump and distillate pump motor.
Regulating the Capacity of Fresh water Generator
Capacity of a fresh water generator means the quantity of fresh water produced by it per day. The capacity of fresh water generator can be varied by reducing or increasing the amount of jacket cooling water to the evaporator. The quantity of jacket cooling water to the evaporator can be adjusted by adjusting the bypass valve provided. When the temperature of jacket cooling water is comparatively low, the quantity to the evaporator to be increased a bit. At the same time cooling seawater pressure to the condenser also to be regulated accordingly.
During very low seawater temperatures, evaporation temperature can falls to a lower value. In that case, adjust vacuum adjusting valve to control vacuum inside the shell. Cooling seawater quantity to the condenser also can be reduced to increase the evaporator temperature. During high seawater temperatures, evaporation temperature can go up. In that case, increase the quantity of seawater to the condenser for reducing evaporation temperature.
Too high evaporation temperature causes scale formation in the heat exchanger. On the other hand, too low evaporation temperature results in seawater carry over which increases salinity of fresh water produced.
The distillate pump discharge to be throttled so that pump should not run dry. The rate of distillate pump discharge and rate fresh water produced in the condenser should match. When distillate pump is not able to extract the freshwater at the rate of production, level of freshwater increases in the condenser and effective cooling area of the condenser reduces. This finally results in reduced evaporation quantity.
Fresh water Generator Stopping Procedure
When ship approaches port, shallow water, etc. it is desirable to stop the fresh water generator. This is because the seawater may contain harmful bacteria which can enter the freshwater produced. Operation of freshwater should be carried out in consultation with bridge watch keeper. Following procedure may be adopted for stopping fresh water generator.
- Slowly open bypass valve for main engine jacket cooling water.
- Ensure that main engine jacket cooling water temperature is within normal limits.
- Close jacket cooling water inlet and outlet valves for the freshwater generator respectively.
- Close the feed water chemical dosing valve.
- Stop the distillate pump and shut discharge valve.
- Switch off salinity meter.
- Close filling valve to freshwater tanks.
- Wait for evaporator shell temperature to drop below 50 deg cel.
- Close the feed water valve to evaporator.
- Stop ejector pump. Shut fresh water generator overboard valve.
- Open the vacuum breaker valve to make shell side pressure equal to atmospheric pressure.
- Open the drain valve of the evaporator to drain all the seawater from the fresh water generator.
Precautions for Operation of Fresh water Generator
- Seawater pressure at the inlet of air ejector must be 3 bar or more.
- The pressure at ejector outlet should not exceed 0.8 bar.
- Never start fresh water generator distillate pump in dry condition.
- Operate jacket cooling water valves to the fresh water generator gradually to avoid thermal shock to the main engine.
- Feed water to be supplied for a few minutes to cool down the evaporator before stopping.
- Never open the drain valve of evaporator before opening vacuum breaker. Otherwise atmospheric pressure causes seawater inside to hit the deflector.
How Scale Formation Occurs in Fresh Water Generator
The performance of fresh water generator reduces with the formation of scales because of reduction in heat transfer efficiency. Three scales which are normally found in fresh water generators are:
- Calcium Carbonate, CaCO3
- Magnesium Hydroxide, Mg(OH)2
- Calcium Sulphate, CaSO4
Calcium carbonate and magnesium hydroxide scale formation mainly depends on the temperature of operation. Calcium sulphate scale formation depends mainly on the density of the evaporator contents or brine. The reaction takes place when sea water heated are:
Ca(HCO3)2 ————> Ca + 2HCO3
2HCO3 ————> CO3 + H2O + CO2
If heated up to approx. 80 degree Celsius
- CO3 + Ca ————> CaCO3
If heated above 80 degree Celsius
- CO3 + H2O ————> HCO3 + OH
- Mg + 2OH ————> Mg(OH)2
Hence if the sea water in the fresh water generator is heated to a temperature below 80 degree Celsius, calcium carbonate scale predominates. If sea water is heated above 80 degree Celsius, magnesium hydroxide scale is deposited.
If the density of evaporator contents is in excess of 96000 ppm, calcium sulphate scales are formed. But fresh water generator brine density is normally 80000 ppm and less. Hence scale formation due to calcium sulphate is not a problem.
Hence it is recommended to operate fresh water generator at its rated capacity, not more. More production of water than rated capacity means higher concentration of brine and more scale formation. Similarly higher shell temperatures result in formation of hard scales which will be difficult to remove. All these together will reduce the plant efficiency drastically.
How to Minimize Scale Formation
Scale formation in fresh water generator can be controlled and minimized by continuous chemical treatment. Polysulphate compounds (like sodium polysulphate) with anti foam is preferred by marine engineers and is extensively used on ships. Their trade name is different, like:
- Vaptreat (by “UNITOR”)
- Ameroyal (by “DREW CHEMICALS”)
These chemicals minimize calcium carbonate scale formation and possibility of foaming. the compound is non toxic, no-acidic, and can be used in fresh water generator producing water for drinking purposes. If would be continuously fed into the feed line using a metering pump or by gravity. Amount of chemical to be dosed depends on the capacity of fresh water produced. Important thing is that this chemical is effective only on low pressure fresh water generators. The sea water temperature to be less than 90 degrees. Fresh water generator chemical treatment to be religiously carried out to maintain its performance.
Faults in fresh water generator
Faults in fresh water generator reduces performance of the system, thereby reducing quality and quantity of freshwater produced on ships. These irregularities must be identified and rectified immediately to ensure that the optimum performance of the fresh water generator is achieved.
Typical faults in fresh water generator are:
Loss of Vacuum or Over-pressure of Shell
The shell pressure of the fresh water generator rises and rate of freshwater produced reduces. The reasons are:
- Air leaks into the evaporator shell in large quantities and air ejector cannot cope.
- The cooling water flow through the condenser is reduced or cooling water temperature is high. This cause saturation temperature and hence saturation pressure within the condenser to rise.
- Malfunctioning of the air ejector.
- Flow rate of the heating medium increased and excess water vapour produced. Since this excess vapours cannot be condensed, shell pressure increases or vacuum falls.
Salt Water Carry Over
Salt water may be carried over in large quantities during operation of the freshwater generator. This is called priming. General reasons of the priming are:
- Level of salt water inside the shell is high. When water level is high agitation due to boiling occurs and salt water may carry over along with the vapours.
- When the salt water brine density is too high, agitation of salt water occurs which results in priming.
- Increased evaporation rate.
Gradual Increase in Level of Brine
For the satisfactory operation of the freshwater generator, a constant level of brine to be maintained in the shell. Brine is the concentrated sea water after liberation of water vapours. This brine is gradually extracted from the shell. Usually this is achieved by the combined air-brine ejector. It extracts air as well as brine from the shell. Any fault in the ejector or brine extraction pump (in some models) cause increase in the brine level.
Increase in Salinity of Freshwater
Possible causes are:
- Brine level inside shell too high.
- Leaking condenser tubes or plates.
- Operation of evaporator near shore with contaminated feed water.
- Shell temperature and pressure too low.
- Increased solubility of CO2 generated from the salt water due to reduced sea water temperature. This dissolved CO2 makes water acidic and conductivity of water increases. Hence salinometer shows increased salinity, which is a measure of conductivity ans not presence of salt.
Oil Purifier
Oil purifiers are used on board ship to condition fuel oil and lubricating oil.
The fuel oil used on ships is normally very thick and viscous at normal temperatures. It is called Class C Marine Bunker oil. It contains a lot of impurities too.
Lubricating oil for diesel engines do get contaminated with carbon deposits, byproducts of oxidation, sludge and metal particles.
The oil to be purified is first allowed to settle in a settling tank. Any large particles will settle out and can be drained every watch. After the oil has time to settle, it is passed through fine meshed wire filters to remove any coarse particles. The oil is then sent to theoil purifier.
The oil purifier makes use of centrifugal force to separate fine solids which cannot be filtered out from the oil.
The oil to be purified is first allowed to settle in a settling tank. Any large particles will settle out and can be drained every watch. After the oil has time to settle, it is passed through fine meshed wire filters to remove any coarse particles. The oil is then sent to theoil purifier.
The oil purifier makes use of centrifugal force to separate fine solids which cannot be filtered out from the oil.
By rotating the bowl at a very high speed of 15000 rpm or so, the fine solids are separated from the oil.
At these high speeds, the shaft balancing, bearings, and vibration damping mechanism is critical. The high speeds can be achieved by worm-and-wheel drive.
The building up of speed during starting up is achieved by using friction pads. To prevent serious damage to the drive in case of seizures or overload, a shear pin, or shear coupling mechanism is installed between the motor drive and the driven gears.
Although the oil purifier is made to be automatically self flushing, it still needs to be dismantled for manual cleaning periodically. On the ship, very often, the purifiers are maintained by the Junior Engineer.
When the Bunker Fuel oil is of very poor quality, the purifiers have to be opened up very often. The fuel oil purifier room is very often oily, slippery, and hot because the fuel oil is heated to temperatures up to 130 degree Celsius.
Although the oil purifier is made to be automatically self flushing, it still needs to be dismantled for manual cleaning periodically. On the ship, very often, the purifiers are maintained by the Junior Engineer.
When the Bunker Fuel oil is of very poor quality, the purifiers have to be opened up very often. The fuel oil purifier room is very often oily, slippery, and hot because the fuel oil is heated to temperatures up to 130 degree Celsius.
Air conditioning
(often referred to as AC, A.C., or A/C) is the process of removing or adding heat from/to a space, thus cooling or heating the space's average temperature.
Air conditioning can be used in both domestic and commercial environments. This process is most commonly used to achieve a more comfortable interior environment, typically for humans or animals; however, air conditioning is also used to cool/dehumidify rooms filled with heat-producing electronic devices, such as computer servers, power amplifiers, and even to display and store artwork.
Air conditioners often use a fan to distribute the conditioned air to an occupied space such as a building or a car to improve thermal comfort and indoor air quality. Electric refrigerant-based AC units range from small units that can cool a small bedroom, which can be carried by a single adult, to massive units installed on the roof of office towers that can cool an entire building. The cooling is typically achieved through a refrigeration cycle, but sometimes evaporation or free cooling is used. Air conditioning systems can also be made based on desiccants (chemicals which remove moisture from the air) and subterraneous pipes that can distribute the heated refrigerant to the ground for cooling.[1]
In the most general sense, air conditioning can refer to any form of technology that modifies the condition of air (heating, cooling, (de-)humidification, cleaning, ventilation, or air movement). In common usage, though, "air conditioning" refers to systems which cool air. In construction, a complete system of heating, ventilation, and air conditioning is referred to as heating, ventilation, and air conditioning (HVAC – as opposed to AC).
Tools
![]() anchor jangkar | ![]() anvil paron | ![]() blade mata pisau | ![]() board papan | ![]() bolt baut |
![]() bottle opener pembuka botol | ![]() broom sapu | ![]() brush sikat | ![]() bucket ember | ![]() buzz saw gergaji bundar |
![]() can opener pembuka kaleng | ![]() chain rantai | ![]() chainsaw gergaji mesin | ![]() chisel pahat | ![]() circular saw blade bilah gergaji lingkar |
![]() drill machine mesin bor | ![]() dustpan pengki | ![]() garden hose selang taman | ![]() grater parutan | ![]() hammer palu |
![]() hinge engsel | ![]() hook pengait | ![]() ladder tangga | ![]() letter scale neraca skala | ![]() magnet magnet |
![]() mortar mortar | ![]() nail paku | ![]() needle jarum | ![]() network jaringan | ![]() nut mur |
![]() palette-knife pisau aduk | ![]() pallet palet | ![]() pitchfork garpu rumput | ![]() planer mesin serut | ![]() pliers tang |
![]() pushcart kereta dorong | ![]() rake penggaruk | ![]() repair perbaikan | ![]() rope tali | ![]() ruler mistar |
![]() saw gergaji | ![]() scissors gunting | ![]() screw sekrup | ![]() screwdriver obeng | ![]() sewing thread benang jahit |
![]() shovel sekop | ![]() spinning wheel alat pemintal | ![]() spiral spring pegas spiral | ![]() spool gulungan | ![]() steel cable kabel baja |
![]() tape selotip | ![]() thread benang | ![]() tool perkakas | ![]() toolbox tas perkakas | ![]() trowel cetok |
![]() tweezers pinset | ![]() vise catok | ![]() welding equipment peralatan las | ![]() wheelbarrow gerobak dorong | ![]() wire kawat |
![]() wood chip serpih kayu | ![]() wrench kunci pas |
Tidak ada komentar:
Posting Komentar